Empowering innovation through advanced technology
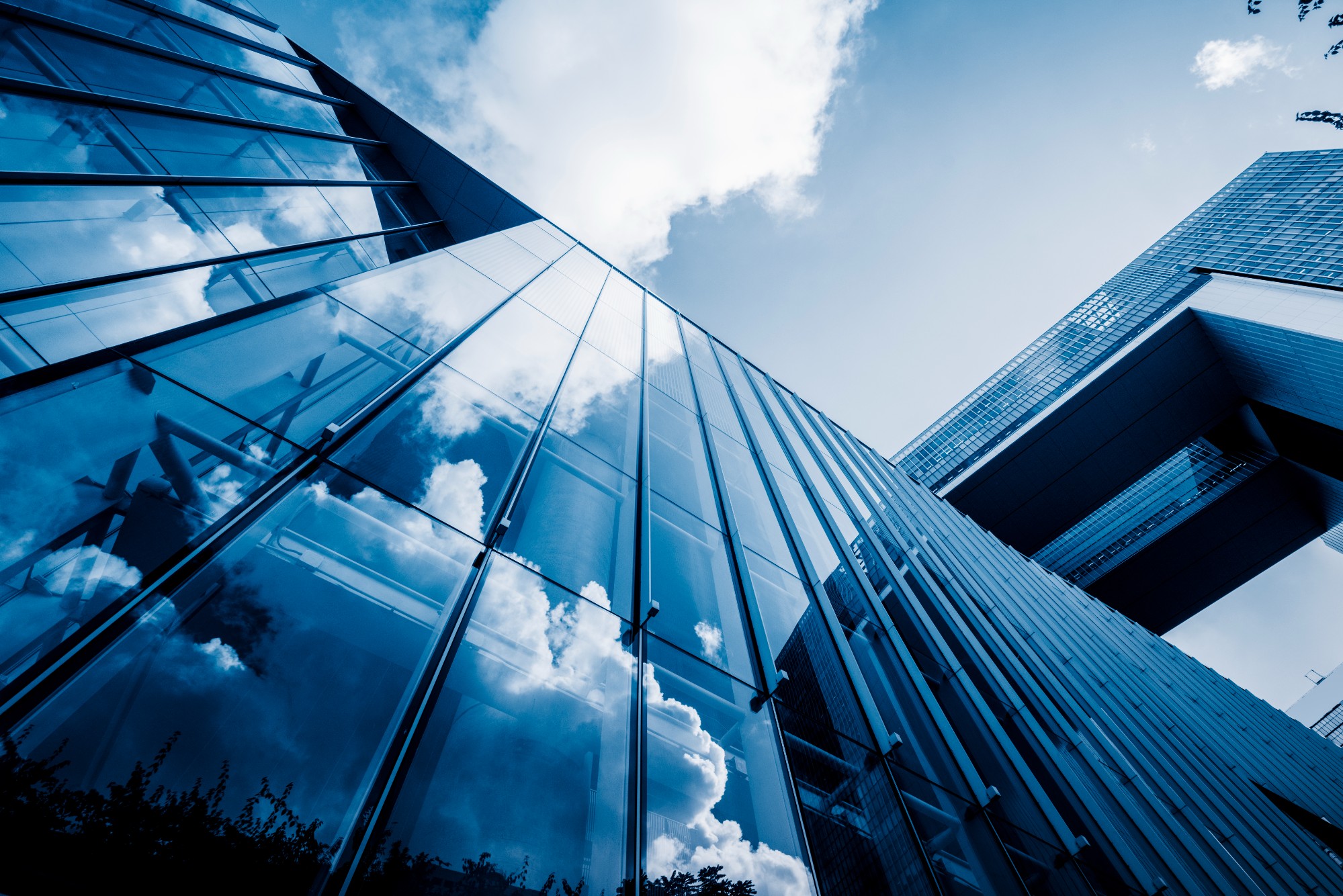
Forbes calls it the most dangerous phrase in business: “We’ve always done it this way.” This expression sums up the construction sector’s reluctance to embrace innovation and technology. It’s understandable why this largely risk-averse industry wants to protect its way of doing things. Their methodologies have worked for decades, so why change now? The difference today is that our sector is facing massive challenges that will only be compounded with time.
There are countless articles about how the construction sector lags behind other industries in technology and innovation. It’s a reluctance fuelled by fears of costs, scale, code and regulatory requirements, and lack of proven test cases. As global demand for housing (in both the public and private sectors) and construction costs continue to grow, the industry must change the way projects are delivered. Sustainability is another significant driver of change as governments and industry leaders look to reduce our footprint on the environment. Technology and innovation can provide solutions to all these pressing issues being felt across the globe.
In provinces like British Columbia, our affordable housing projects have to meet the strict efficiency requirements of the BC Energy Step Code. Through innovative measures like upgraded HVAC technologies and solar-ready roofs, we can exceed those guidelines and work towards making these standards the rule, not the exception.
A better way to build
The construction industry is full of untapped potential. More technologies are coming online that streamline workflows, automate production, improve safety, reduce costs, and increase performance efficiency. Many of these tools are already here. The recent news of Nexii Building Solutions attaining a valuation of US$1 billion is a testament to how technological advancements can change the conversation. The company became the fastest in Canada to reach “unicorn status” and has partnered with restaurant chains including Starbucks, Popeyes, and A&W to provide construction materials that can reduce a building’s emissions by 30%.
Nexii’s signature product is Nexiite, a revolutionary material that provides an alternative to concrete for floors, walls, and roofs. Considering that cement – an essential ingredient for concrete – accounts for 7% of the world’s CO2 emissions, this innovative component is a game-changer in the industry. These advancements are crucial to accelerate the construction of sustainable and cost-efficient buildings, but they also require the collective support and commitment of our industry to ensure large-scale adoption and usage.
Nomodic has partnered with Nexii to install two eco-friendly restaurant projects, and recently signed a three-year Master Service Agreement (MSA) to be a preferred and certified installer for the company moving forward. As our company continues to create cost-effective and sustainable solutions for clients, it’s imperative we stay current with new industry innovations and continue to engage like-minded, green technology-driven companies that are bringing innovative solutions to the market.
The advancements in technology and innovation being pioneered by companies like Nexii contribute to our industry’s biggest needs – creating faster timelines, providing safe living spaces, improving safety, reducing material and construction costs, and minimizing the impact on the environment. Some of these innovations allow us to envision and virtually create a project before a single power tool is turned on.
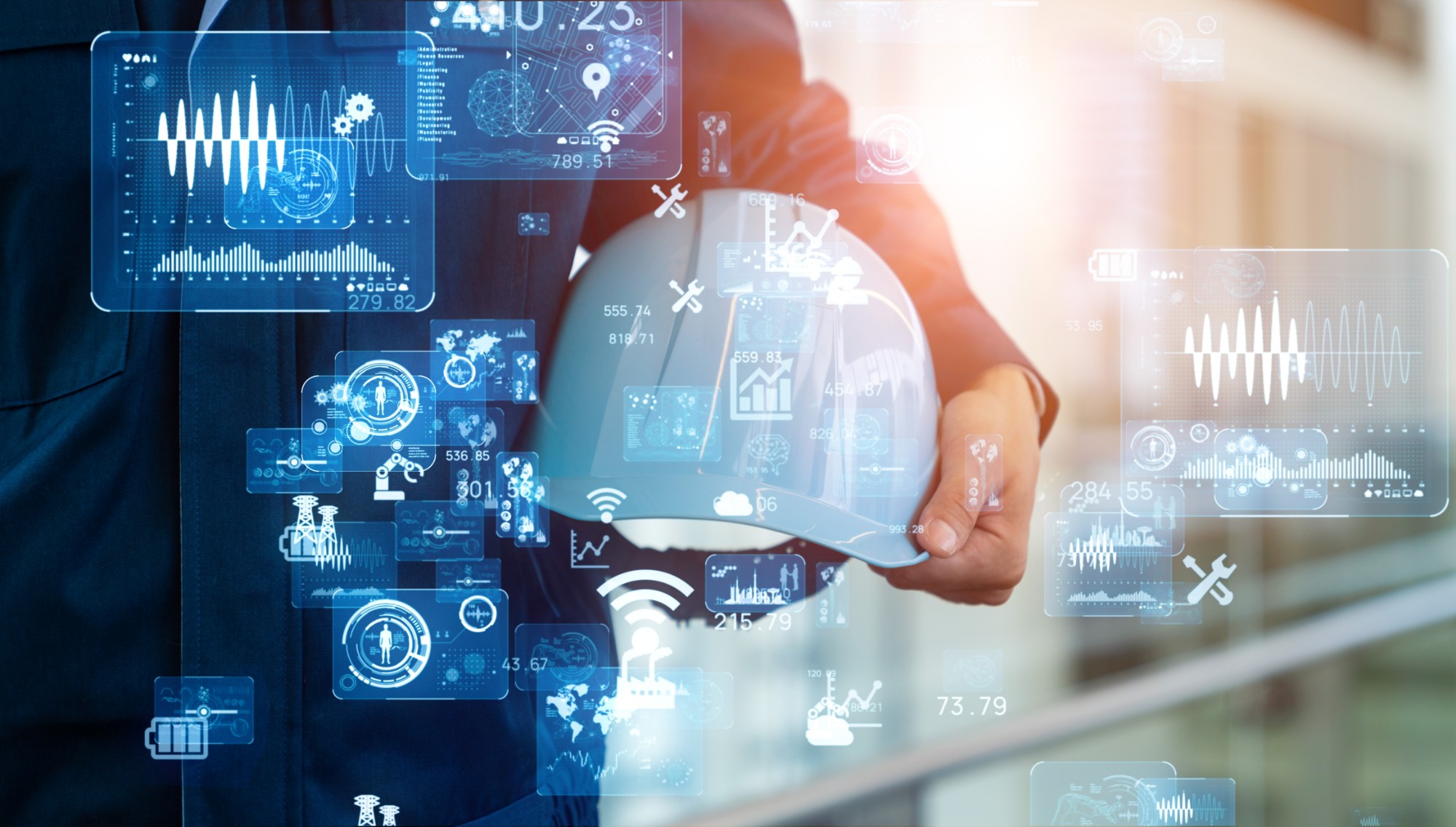
Building with the end in mind
Everyone remembers the old adage, “measure twice, cut once.” Through technology like Building Information Modelling (BIM), a project can be mapped out throughout its entire life cycle. Efficiencies are built into the process while the model serves as the “one source of truth” for consistency across all contributors.
Clients see what their project will look like and if factors like material choices and site requirements are feasible. Best of all, the major stakeholders can be involved (owners, architects, contractors, fabricators, engineers, and more) from the very beginning. Important decisions that affect project costs can then be made early in the process. According to the National Institute of Building Sciences, the lack of this kind of synergy costs owners $15.8 billion annually. Using BIM allows greater control over issues like cost overruns, material quality, and change orders.
In the case of Nomodic’s offsite construction process, there is an opportunity to build in elements of repeatability where prefabricated components can be used across multiple projects to reduce project costs and deliver projects faster. Utilizing designs from existing 3D libraries and methods of standardization doesn’t mean limiting choice or creativity. It allows a company to offer different building methods that provide a broader spectrum of material components that reduce or remove limitations of any one specific offsite methodology.
Our role as a project integrator allows us to provide clients with unrivalled access to construction technologies and fabrication capacity. We can access a wide variety of fabricator partners and premium-quality materials from across North America, like Nexiite or volumetric wood or steel, to provide developers with products that suit a particular building site. We can mix multiple technologies to provide hybrid solutions and generate value for the client, instead of being confined to just one construction methodology.
There are still more tools that can be added to the box
As the demand for new construction grows, the sector must continue to embrace new technologies to keep up. Through digitization, it has become much easier to see how a project will come together before construction even begins. Each phase can be improved by using technological advancements and innovation, from computer modelling to construction and operation to repurposing and demolition. Greater operational efficiencies also lead to less construction waste. For Nexii, combining clean manufacturing, flat-pack transportation, and rapid onsite assembly leads to near-zero construction waste.
There is a lot more on the horizon to get excited about:
- In Ontario, Canada, six apartment buildings will be constructed using 3D technology. The project grew out of an international competition to design multi-storey buildings for $100 per square foot using new technologies and processes. The structures will be built using a combination of modular and other prefabricated construction methodologies.
- As the construction sector continues to grapple with a shortage of skilled labour, a Toronto startup -Promise Robotics- is leveraging advances in automation, advanced manufacturing, cloud computing and artificial intelligence (AI) to introduce a robot workforce. The company is looking to propel sustainable construction by accelerating projects through greater performance efficiency and flexibility.
Embracing new technologies can go a long way towards improving the construction sector’s bottom line. A McKinsey Global Institute report suggests that being more progressive/proactive with new technologies could add another US$1.6-trillion to the US$10-trillion in economic activity. It’s identified as one of the key factors of increasing productivity.
The path is clear. Seizing the opportunities of today can only lead to a brighter tomorrow.